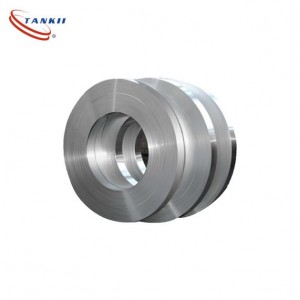
Monel K400 and K500 are both members of the renowned Monel alloy family, but they possess distinct characteristics that set them apart, making each suitable for different applications. Understanding these differences is crucial for engineers, manufacturers, and material enthusiasts looking to make informed material selection decisions.
The most fundamental difference lies in their chemical composition. Monel K400 is primarily composed of nickel (around 63%) and copper (28%), along with small amounts of iron and manganese. This simple yet effective alloy composition contributes to its excellent corrosion resistance and good mechanical properties at room temperature. In contrast, Monel K500 builds on the base of K400 by adding aluminum and titanium. These additional elements enable K500 to undergo a precipitation hardening process, which significantly enhances its strength and hardness compared to K400.
This compositional disparity directly impacts their mechanical properties. Monel K400 offers good ductility and formability, making it easy to fabricate into various shapes. It has a relatively lower tensile strength, which is suitable for applications where flexibility and ease of machining are priorities, such as in the production of marine piping systems and general-purpose corrosion-resistant components. Monel K500, after precipitation hardening, exhibits much higher tensile and yield strengths. It can withstand greater mechanical stress, making it ideal for applications that demand robust components, like pump shafts, valve stems, and fasteners in heavy machinery and marine vessels.
Corrosion resistance is another area where the two alloys show differences. Both Monel K400 and K500 offer excellent resistance to a wide range of corrosive media, including seawater, mild acids, and alkalis. However, due to its higher strength and the formation of a more stable protective oxide layer during precipitation hardening, Monel K500 often demonstrates enhanced resistance to stress corrosion cracking, especially in environments with high chloride content. This makes K500 a preferred choice for components that are not only exposed to corrosive elements but also need to endure mechanical stress simultaneously.
In terms of applications, Monel K400 is commonly used in the marine industry for components such as condensers, heat exchangers, and seawater piping, where its corrosion resistance and formability are valued. It is also employed in the chemical industry for handling non-aggressive chemicals. Monel K500, on the other hand, is utilized in more demanding applications. In the oil and gas sector, it is used for downhole tools and subsea equipment, where high strength and corrosion resistance are essential. In the aerospace industry, K500 components can be found in parts that require both strength and resistance to environmental corrosion.
Post time: Jul-16-2025