Introduction to Heating Alloys
When selecting materials for heating elements, two alloys frequently come into consideration: Nichrome(Nickel-Chromium) and FeCrAl(Iron-Chromium-Aluminum). While both serve similar purposes in resistive heating applications, they possess distinct characteristics that make them suitable for different environments and applications. Understanding these differences is crucial for choosing the right material for your specific needs.
1.Composition and Basic Properties
Nichrome is a nickel-chromium alloy typically containing 80% nickel and 20% chromium, though other ratios exist. This combination provides good resistance to oxidation and maintains strength at high temperatures. Nichrome alloys are known for their formability and consistent performance across a wide temperature range.
FeCrAl alloys, as the name suggests, are primarily composed of iron (Fe) with significant additions of chromium (Cr) and aluminum (Al). A common composition might be 72% iron, 22% chromium, and 6% aluminum. The aluminum content particularly enhances the alloy's high-temperature performance and oxidation resistance.
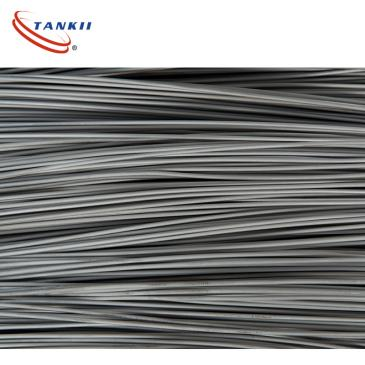
2.Temperature Performance
One of the most significant differences lies in their maximum operating temperatures:
- Nichrome typically operates up to about 1200°C (2192°F)
- FeCrAl can withstand temperatures up to 1400°C (2552°F)
This makes FeCrAl superior for applications requiring extreme heat, such as industrial furnaces or high-temperature laboratory equipment.
3.Oxidation Resistance
Both alloys form protective oxide layers, but through different mechanisms:
- Nichrome forms a chromium oxide layer
- FeCrAl develops an aluminum oxide (alumina) layer
The alumina layer in FeCrAl is more stable at very high temperatures, providing better long-term protection against oxidation and corrosion. This makes FeCrAl particularly valuable in environments with potential corrosive elements.
4.Electrical Resistivity
Nichrome generally has higher electrical resistivity than FeCrAl, which means:
- Nichrome can produce more heat with the same amount of current
- FeCrAl may require slightly more current for equivalent heating
However, FeCrAl's resistivity increases more significantly with temperature, which can be advantageous for certain control applications.
5.Mechanical Properties and Formability
Nichrome is generally more ductile and easier to work with at room temperature, making it preferable for applications requiring complex shapes or tight bends. FeCrAl becomes more ductile when heated, which can be advantageous during manufacturing processes but may require special handling at room temperature.
6.Cost Considerations
FeCrAl alloys typically cost less than Nichrome because they replace expensive nickel with iron. This cost advantage, combined with superior high-temperature performance, makes FeCrAl an attractive choice for many industrial applications.
Why Choose Our FeCrAl Products?
Our FeCrAl heating elements offer:
- Superior high-temperature performance (up to 1400°C)
- Excellent oxidation and corrosion resistance
- Longer service life in extreme conditions
- Cost-effective alternative to nickel-based alloys
- Customizable solutions for your specific application needs
Whether you're designing industrial furnaces, heating systems, or specialty equipment, our FeCrAl products provide the durability and performance required for demanding environments. Contact us today to discuss how our FeCrAl solutions can meet your heating element requirements while optimizing your operational costs.
Post time: Apr-09-2025